History of Clay Industry in India
A German missionary had set up the first tile factory at Mangalore in 1860 after they found large deposits of clay by the banks of the Gurupura and Nethravathi rivers. It was called Basel Mission tile factory, and was the first ever tile factory in India, located on the banks of the Nethravathi River, near Morgan’s Gate. Since then the industry flourished in India. Several other tile factories came up in the years that followed. Mangalore tiles, which is also known as Mangalorean tiles are a type of tiles native to the city of Mangalore, in India. These red tiles, prepared from hard laterite clay, are in great demand throughout India, Myanmar, Sri Lanka, the Far East and are even shipped to East Africa, the Middle East, Europe, and Australia. These were the only tiles to be recommended for Government buildings in India during the British regime as these are very popular form of roofing and are preferred over concrete due to its excellent quality.
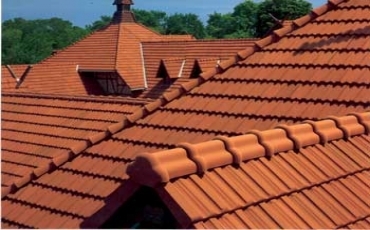
Quality and Usage of Clay Tiles
They provide excellent ventilation especially during summer and aesthetically as well. These red colored clay tiles, unique in shape and size are so famous and exported to all the corners of the world. They are unique and are made or available in different size and shapes depending on the users need. These tiles are not only eco-friendly but also cheap, durable and costs only one third that of cement. Some of the buildings which are 100 yrs old still have tile roofing in excellent condition. These tiles are suited for regions experiencing heavy rainfall as water drains easily and fast. The Mangalore tiles are generally placed at forty five degree slant. The tiles get their robust red color due to the high proportion of iron compound found in the laterite clay. A tile weighs about 2 kilograms to 3 kilograms .These kind of tiles are most popularly used in our Kerala & Goa.
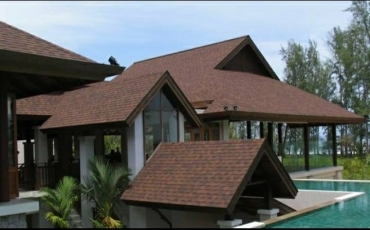
Tile Preparation Process
First part is to collect enough clay and place it in a mold and is cut to exact measurement. Then that rectangular piece of clay with exact length and thickness is placed on another machine which puts the factory logo and shapes it into a tile. Then with hand any extra clay is removed and sent to be carried for firing and later glazing. It is a very delicate and detailed process starting from collection of clay to the final product to be fired. Once fired and glazed it is ready and is stored for shipping.
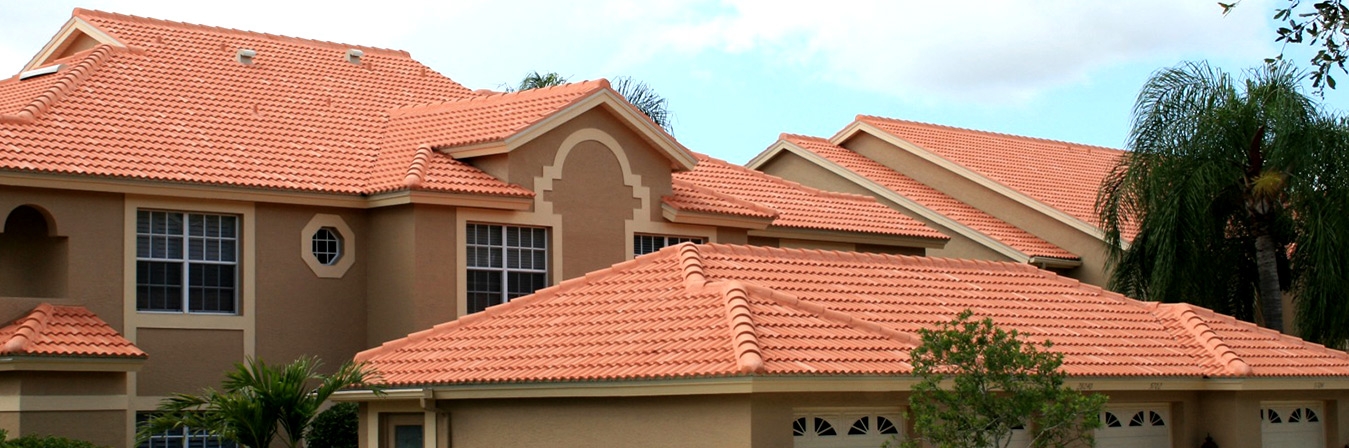